
Applications
Passenger Car Development
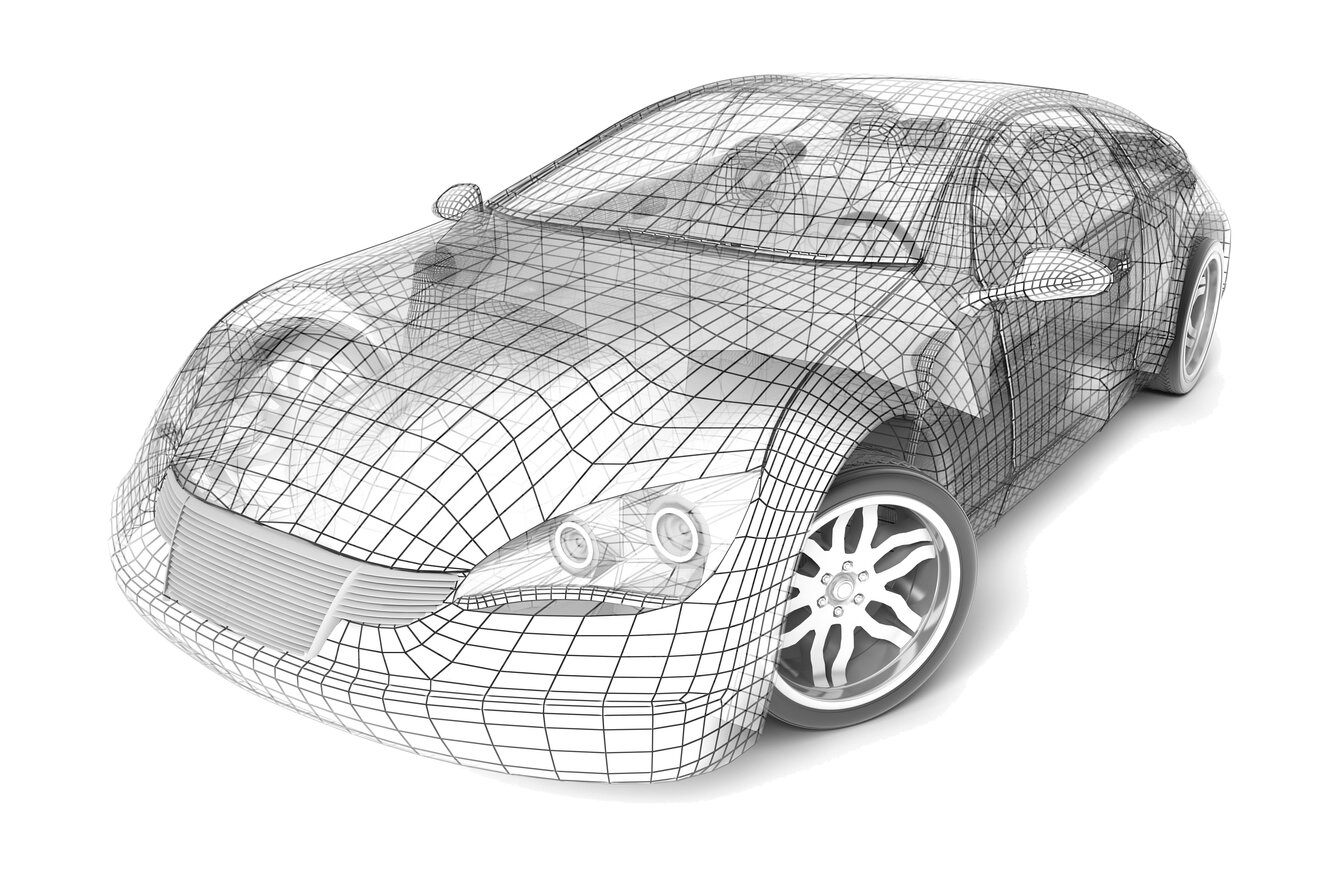
Discover our exemplary applications
Car bodies are complex structures with a high number of contact interfaces. A typical approach for a durability analysis is to apply external loads on a linear inertia relief calculation. With this method contact stresses and resonances within the structure are neglected. In a more advanced approach the car body is included as a flexible structure in a multibody system and contact interaction is accounted with MAMBA.
For a local durability analysis, as in the depicted example of a rear battery carrier, the user can select contacts in the area of interest. With MAMBA the fatigue results for the typically highly loaded spot welds show improved correlation to physical testing.
If the complete car body shall be assessed, then MAMBA can automatically identify all relevant contacts based on reference simulations. This simulation approach allows an accurate durability analysis considering structural vibrations and nonlinear contacts.
Benefits
- Automated detection of relevant contacts in complex elastic structures
- Influence of structural vibrations considered
- Improved fatigue analysis process for car bodies

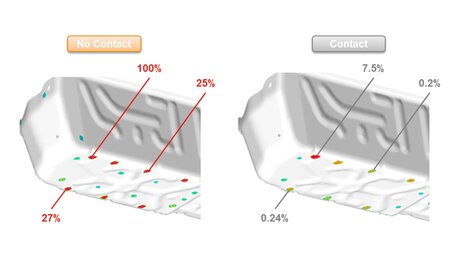
Powertrain components, like engines and gearboxes, usually have a high number of bolted contact surfaces. These non-linear interactions between parts influence the stresses under load as well as the vibration behavior.
The depicted example of a transfer case shows the stress distribution on the housing flange in assembled state. By including this housing as a flexible structure in a powertrain dynamic simulation, the time-dependent stresses within the housing and contact stresses can be evaluated. Based on these results, the durability of the housing and the leak-tightness can be analyzed.
A torsional damper bolted on a crank shaft is highly dynamically loaded. In areas where the contact pressure is reduced during peak-loads, fretting corrosion can be observed. For the depicted investigation a full load run-up simulation was carried out with a crank train model including MAMBA for the contact interface between crankshaft and visco-damper. Based on the obtained results critical speeds, where the contact pressure reduces in the areas of the wear pattern, were identified.
Benefits
- Analysis of leak-tightness of bolted housings
- Evaluation of fretting corrosion due to dynamic loads
- Evaluation of full rpm range to include possible resonance effects
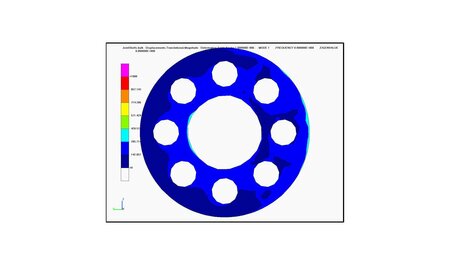
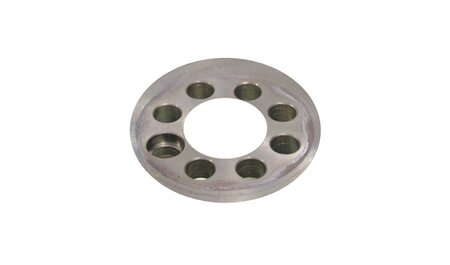
The battery of a passenger car is vibrating due to the road excitation. Because of the mass of the battery these vibrations lead to high structural loads within the supporting structure. Thus a correct dynamic model including the nonlinear contact interactions at the spot welded flanges becomes necessary for a reliable durability analysis.
In this example model of a battery bracket the contact interactions within the spot welded flanges of the battery bracket and the surrounding area were included with MAMBA. In the linear model the loads are only transferred via the spot models leading to unrealistically high damage values in several locations. The supporting effect of contacts results in a different load path which leads to reduced damage values in several spot welds and increased damage values in some spot welds.
Benefits
- Realistic vibration response due to correct load path
- Realistic damage evaluation of spot welded structures
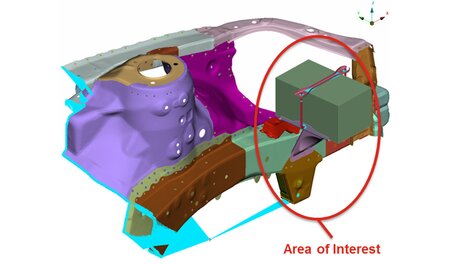
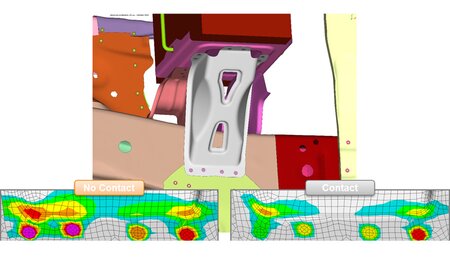
The slam of a car door is a dynamic process which influences the durability of the door structure. In this simulation example the flexible door was accelerated to reach a defined impact speed. A correct modelling of the sealing stiffness and the latch mechanism is necessary to reproduce the peak loading.
The analysis of the linear model without contact interfaces indicated unrealistic penetration of some metal sheets in the area of the latch. By simulating the door slam with activated MAMBA contacts, a realistic loading could be reproduced. Both simulation results were utilized as input for a subsequent fatigue assessment. A comparison of the highest damaged spot welds emphasizes the necessity of including contacts for a door slam simulation.
Benefits
- Realistic loading of door structure for fatigue analysis
- Reduced simulation time compared to explicit finite element solvers
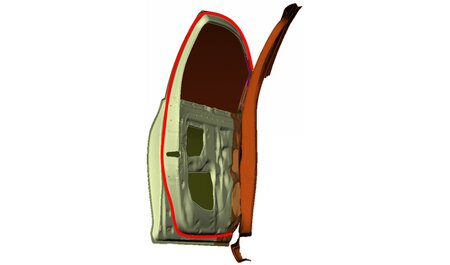
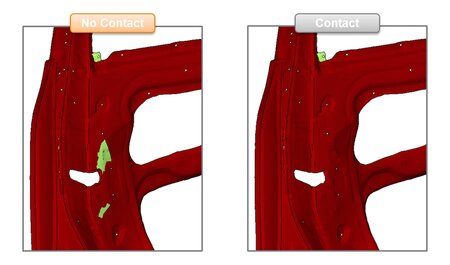
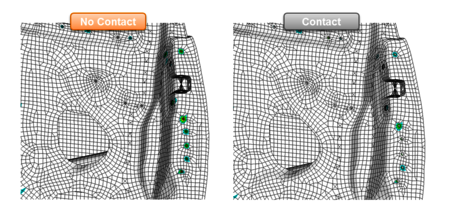
Commercial Vehicle Development
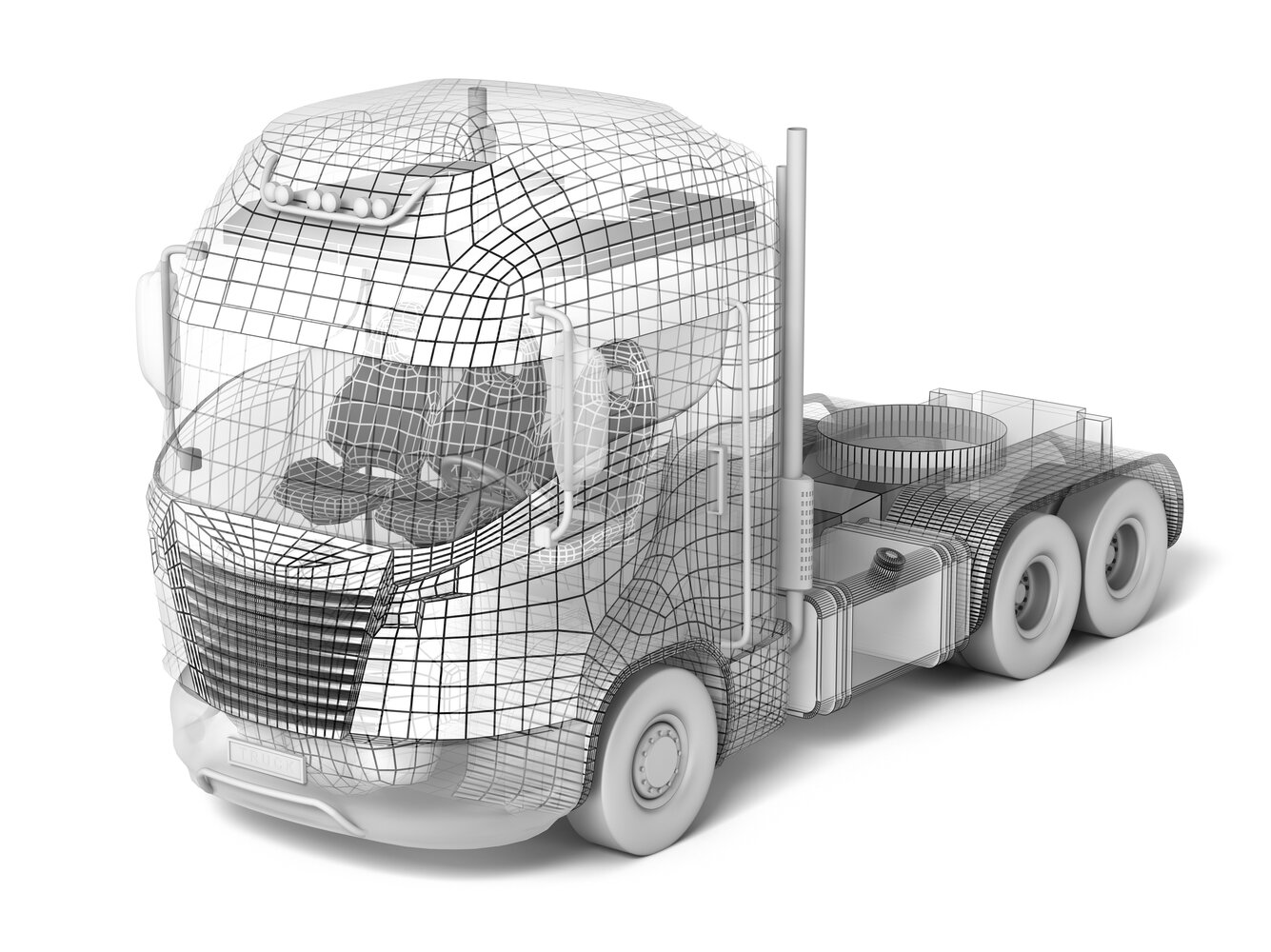
Discover our exemplary applications
The slam of a truck door is a dynamic process which influences the durability of the door. In this simulation example the flexible door was accelerated to reach a defined impact speed. A correct modelling of the sealing stiffness and the latch mechanism is necessary to reproduce the peak loading.
The analysis of the linear model without contact interfaces indicated unrealistic penetrations of the stiffeners in the hinge area. By simulating the door slam with activated MAMBA contacts, a realistic loading could be reproduced. Both simulation results were utilized as input for a subsequent fatigue assessment. A comparison of the highest damaged locations emphasizes the necessity of including contacts for a door slam simulation.
Benefits
- Realistic loading of door structure for fatigue analysis
- Reduced simulation time compared to explicit finite element solvers
Attachment parts connected to the truck frame are vibrating due to road or powertrain excitations. Because of the mass of the attached parts these vibrations lead to high structural loads within the area of the bolted flange between frame and attachment part. Thus a correct dynamic model including the nonlinear contact interactions is necessary for a reliable durability analysis.
In this example model of a side rail attachment the contact interaction between the side rail and the bracket was included with MAMBA. The dynamic response analysis results indicate a shift of the natural frequencies due to a stiffer coupling. In the linear model the loads are only transferred via the bolt models, which causes unrealistically high local damage. The supporting effect of contacts with MAMBA results in a distribution of the loads and thus the damage is reduced significantly.
Benefits
- Improved vibration response of attachment parts
- Realistic damage evaluation of bolted structures
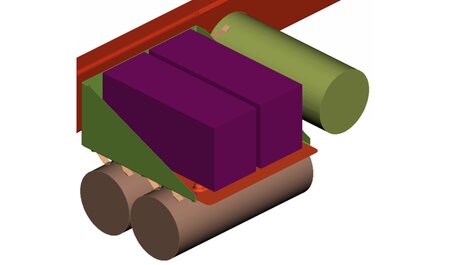
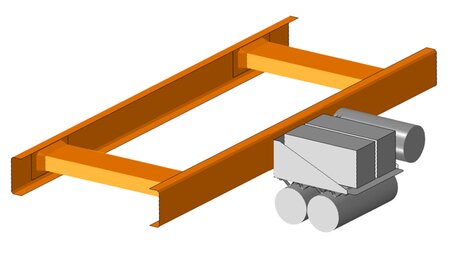
During the development process of a truck frame, the global stiffness and the durability performance are important design requirements.
Commercial vehicle frames typically have a high number of bolted contact areas. Utilizing linear FE methods is convenient, but does not correctly reproduce the local loading in certain areas of the contacting flanges. This may lead to unrealistic fatigue assessment results.
For a novel lightweight frame segment concept the contact interfaces were detected and the important contact areas identified. The load simulation results including contact analysis with MAMBA provided the input for the subsequent fatigue assessment.
A comparison of the results stemming from a linear FE analysis and the results obtained utilizing the MAMBA simulation process shows significant differences in the predicted damage distributions.
Benefits
- Improved accuracy of fatigue assessment results
- Durability performance evaluation of bolted contact areas
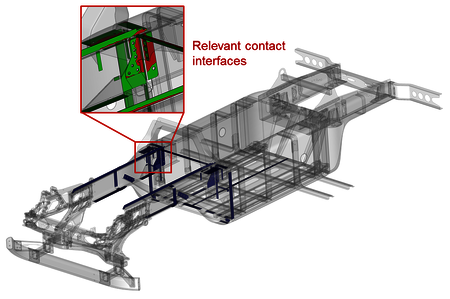
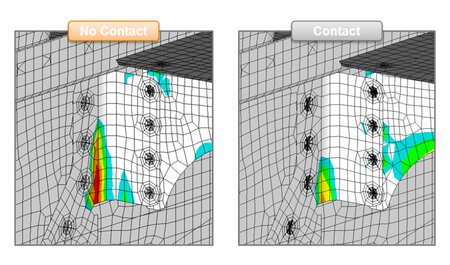
During driving the suspensions multi-leaf spring is a dynamically loaded component. The sliding friction interaction between each leaf is a relevant damping mechanism for the vehicle.
By utilizing MAMBA it is possible to model e.g. trunnion springs that reproduce the correct nonlinear static and dynamic characteristics. Measurements on a typical spring type proved the high accuracy and predictability of this model.
Finally the spring model was integrated into a full vehicle to facilitate ride and handling simulations with improved result quality.
Benefits
- Accurate consideration of the interaction between the leafs of trunnion springs
- Improved dynamic full vehicle simulation
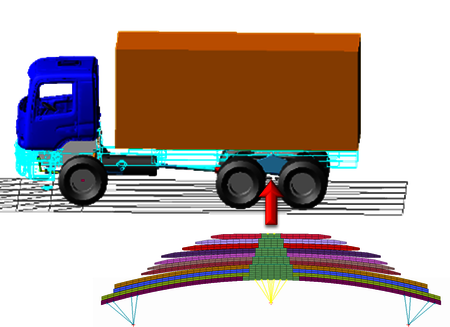
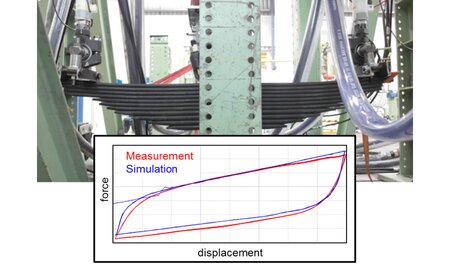